Talc (Soapstone) Mg3Si4O10(OH)2

Talc, Hydrous magnesium silicate Mg3Si4O10 (OH)2 is a hydrous magnesium silicate mineral with a chemical composition of Mg3Si4O10(OH)2. Although the composition of talc usually stays close to this generalized formula, some substitution occurs. Talc, a mineral made up mainly of the elements magnesium, silicon, and oxygen. As a powder, it absorbs moisture well and helps cut down on friction, making it useful for keeping skin dry and helping to prevent rashes.
Fluorite comes in a wide range of colors and has subsequently been dubbed “the most colorful mineral in the world”. The most common colors are purple, blue, green, yellow, or colorless. Less common are pink, red, white, brown, black, and nearly every shade in between. Color zoning or banding is commonly present. The color of the fluorite is determined by factors including impurities, exposure to radiation, and the size of the color centers.
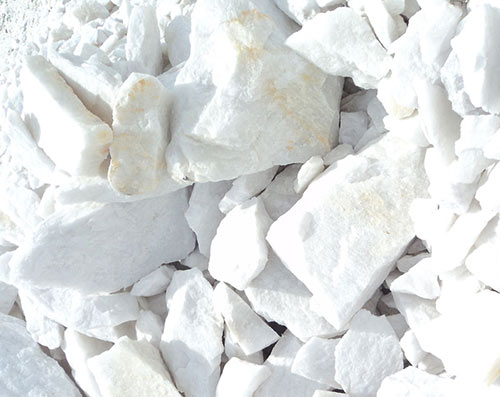
Typical Applications
Talc is used in many industries, including paper making, plastic, paint and coatings, rubber, food, electric cable, pharmaceuticals, cosmetics, and ceramics. A coarse grayish-green high-talc rock is soapstone or steatite, used for stoves, sinks electrical switchboards.
Ground talc makes talcum powder. The massive variety (soapstone) is used for sinks, table tops, etc. Soapstone found a use in Babylonian days when signature cylinder seals were often carved from it.
The Egyptians also used it as a base for some of their blue faience figurines, which were then fired to fuse the glaze. California Indians also used it as sculpture material.
Physical Properties
- Ceramic grade (Coarse, medium & fine)
- Cosmetic grade
- Paint grades
- USP grade
- Soapstone grade
- Micronized grade
- Finely ground grade
Paints
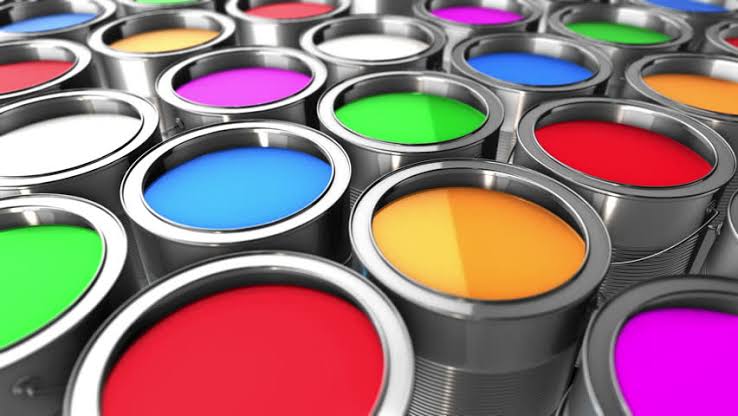
Some of the important properties of Talc used in paint are colour, fineness of grind, oil absorption, chemical inertness and resulting viscosity. Talc helps to impart integrity, reinforce paint films control viscosity and prevent sagging of paint films. It improves suspension and prevents settling of solids at the bottom of the paint container. Because talc is very soft (1 on MOHS hardness scale), it causes only minimal abrasion to process and application equipment. It disperses readily in both aqueous and solvent-based paints. Talc having a surface area greater then 12 m2/g is used for gloss control when an exact degree of Sheen or luster is required. Omtalc has the ability to fulfill all major criterions for the paint industry. Our experts from Pakistan & abroad can assist you in delivering custom made talc for all your production needs. OMGLOSS exhibits following characteristics.
- Whiteness
- Platy Particle shape
- Low oil absorption
- Pacifying power
- Pacifying power
PLASTICS & COMPOUNDING
Talc is important functional filler for compounded thermo-plastic and thermo set polymers. Because of its platy particle shape & purity is used in plastic primarily as reinforcing filler. It increases the stiffness of polypropylene by 80% at a 20% loading and by 150% at a 40% loading. It also increases the heat resistance of polypropylene, reduces mould shrinkage, improves melt theology, and reduces moulding cycle time. Compared to other reinforcing fillers, such as fibreglass, mica, talc is much less abrasive. It gives polypropylene superior low-temperature shock resistivity. In polyethylene film talc is used as an anti-block agent, an additive that roughens the surface of tacky film to prevent it from adhering to itself. Loading levels range from 0.5 to 1.0%.
In vinyl talc is used to improve the hot strength of profile extrusions and to reduce the shrinkage of floor tile. Fine particle size grades are used as nucleating agents for semi-crystalline polyolefin’s, nylon, polyesters, and chlorinated polyethylene. Talc can be used in polyolefin’s at loading levels ranging from 1 to 50% by weight. Talc particles may be described as a series of very small plate-shaped particles which, when aligned, tend to make possible a finished part with improved physical properties. The nature of the particle size & shape will tend to produce slip or a form of lubricant. It is somewhat difficult to disperse in conventional plastic mixing equipment due to overall tendency for more bulking. The material is less sensitive to pH changes; therefore, it can be used in applications where minor acidity is a problem. Talc, as filler for plastics, has some special applications.
Generally, it is used not as the sole filler in moulding formulae but in combination with other filler materials. It facilitates removal from moulds, helps achieve a better sheen or gloss on parts, and lowers the extrusions die wear through its lubricating effect. It is also an effective anti-blocking agent. Talc promotes better fire retardancy and aids in processing and final application of various plastic sealants and mastics. It is also useful as an aid in certain colour applications, as filler for parts in contact with acids, and as a viscosity modifier to accomplish some improvement of overall finished product physical properties. OMPLAS exhibits following characteristics:
- Platy particle shape.
- Whiteness
- Chemical inertness
- Low iron content
- Electrical resistivity
- Super fine particle size
- Low abrasion
- Powder bulk density
CERAMICS
A major consumer of Industrial minerals, the Ceramic industry (especially Asia) uses Talc for “body” and glazing of: Wall tiles, Sanitary Ware, Electrical Insulating (Steatite Talc) Porcelain Dinner Ware. The talc used is generally of 80 ~ 93% whiteness and 200 – 300 mesh. The formation of enstatite as talc disassociates during firing produces high thermal expansion bodies, which results in glazes being put into compression and thereby minimizes crazing. Low moisture expansion bodies are produced, which results in good resistance to delayed crazing. The massive nature of the talc aids in dry pressing and in preparation of good casting slips. Low firing temperatures are possible. The shrinkage and absorption properties of bodies are fairly constant over a wide temperature range. Good white fire bodies are possible. Glazes of unusual brilliance and attractiveness can be fitted readily to high-talc bodies.
Talc is also used in steatite bodies, which are manufactured into high-frequency electric insulators, a segment of the ceramic white wares market. A minor use of talc is as an additive in dinnerware bodies composed of clay, flint and feldspar. Compromising as much as 6% of such bodies, Omcera provides greatly improved craze resistance. OMCERA exhibits the following characteristics.
- Uniform Chemical composition
- Constant amount of shrinkage on firing.
- Fired colour.
- Particle size distribution.
PAPER
One of the major consumers of talc is the paper industry (especially Europe & Japan.) As paper filler talc has a minimal negative effect on sheet strength but improves ink receptivity. It also reduces gloss but enhances opacity & brightness. The main reason for the growth of talc consumption in paper is the availability of high quality micronized talc. When Talc is used as a Titanium dioxide extender in paper it has a distinct weight advantage, a specific gravity of 2.8 vs. 4.2 for TiO2. This advantage becomes more important as postal rates increase.
The unique property of preferentially wetting oily substances in the presence of water makes talc extremely effective in pitch control. Pitch & other oleo resinous components of paper pulps cause serious manufacturing problems if they are not controlled. Talc micronized to a surface area of 12m2/g or more, absorbs the pitch and helps prevent accumulations that would otherwise deposit on the rolls, wire, and other parts of the paper machine. The talc products can be used to pigment latex, starch, or alpha protein coating colors. Ultra fine talc products can be used with clay, calcium carbonate, and titanium dioxide pigments to control rheological properties, calendaring, gloss, ink holdout, opacity & brightness. OMFILL exhibits the following characteristics.
The talc products can be used to pigment latex, starch, or alpha protein coating colors. Ultra fine talc products can be used with clay, calcium carbonate, and titanium dioxide pigments to control rheological properties, calendaring, gloss, ink holdout, opacity & brightness. OMFILL exhibits the following characteristics.
- Whiteness
- Brightness
- Controlled top size
- Platy particle shape
- Pacifying power
- Low abrasion
- m median)mParticle size (8 to 12
- Surface Area
- Whiteness
- Brightness
- Low Abrasion
- Particle size
- Good dispersion without surfactants
CERAMICS
The product Omcos has been formulated by Eshal Industries Minerals with high purity talc’s after careful sorting and hand picking. In cosmetic industry Omcos is used in baby and body powders, facial products, anti-perspirant sticks and various types of creams and lotions. The quality of talc that can be used in cosmetic application has following characteristics.
- Quartz Content (1% maximum, may be lowered to 0.1% maximum)
- Tremolite Content (0.1 maximum)
- Loss on Ignition (6.0% maximum at 10000C)
- Neutral pH.
- Acid soluble substances (2% maximum)
- Water soluble substances (1% maximum)
- Arsenic Content (3ppm maximum)
- Lead Content (20ppm maximum)
- Odor, slip, lubricity, particle size, and whiteness according to costumer specification.
Different grades of Omcos are as follows:
PHARMACEUTICAL:
OMTALC has been in very great demand by the Pharma industry due to its purity, thermal and chemical inertness. Multinational companies like Roche, Glaxo Smith Kline, and Merck Marker have been using OMPHARM since it was introduced.
FILLERS & COATINGS:
Textile sizings are made up of a binder, starch, glue, or synthetic polymer together with mineral powders referred to as weight-adding agents. Finishing agents are employed to improve web impregnation, appearance, dye receptivity, to provide temporary sizing, and to add weight.
- Dry Fire extinguishing powder.
- Cereal polishing.
- Bleaching agent.
- Floor Wax.
- Water filtration.
- Leather treatment.
- Shoe polish.
- Welding rod coating.
- Printing Ink.
- Casting for Iron ore in the direct reduction process.
- Jointing Compounds.
- Foam / Rubber.
- Chewing Gum.
- Animal Feed.
- Soaps Manufacturing